在精密机械加工机器人零件的过程中,刀具的选择和使用需要综合考虑零件材料、加工工艺、加工精度等多方面因素,以下是一些要点:
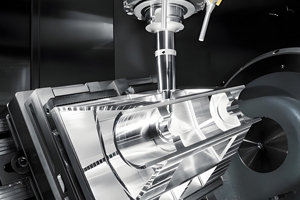
# 刀具的选择
- **根据零件材料选择**:不同的零件材料需要不同的刀具材质来进行有效加工。例如,钢件加工常用硬质合金刀具,其硬度高、耐磨性好,能承受较高的切削温度。对于铝合金等有色金属,可选用金刚石刀具或PCD刀具,这类刀具具有极高的硬度和锋利度,能实现高精度、高效率切削,获得良好的表面质量。而加工钛合金等难加工材料时,则宜采用含钴高速钢刀具或涂层刀具,涂层刀具通过在刀具表面涂覆一层或多层耐磨、耐高温的涂层,如TiN、TiAlN等,可提高刀具的硬度、耐磨性和润滑性,减少刀具与工件之间的摩擦,降低切削力和切削温度。
- **根据加工工艺选择**:不同的加工工艺对刀具有不同的要求。在铣削加工中,对于平面铣削,可选用端铣刀,其刀齿分布在刀具的端部和圆周上,能进行大面积的切削,效率较高。对于轮廓铣削和型腔铣削,则常使用立铣刀,它的圆柱面上有刀齿,端部也可进行切削,能实现复杂形状的加工。在钻孔加工中,要根据孔径和孔深选择合适的钻头,如普通麻花钻适用于一般的钻孔加工,而对于深孔加工,则需使用专门的深孔钻,以保证钻孔的精度和直线度。在车削加工中,外圆车刀用于加工零件的外圆柱面,内孔车刀用于加工内孔表面,而螺纹车刀则用于加工各种螺纹。
- **根据加工精度选择**:对于高精度的机器人零件加工,需要选择精度高、刚性好的刀具。例如,在加工机器人的关节轴类零件时,为保证轴的圆柱度和尺寸精度,可选用高精度的微调镗刀,其能够精确调整刀具的切削尺寸,实现微米级的加工精度。在加工一些具有高精度表面粗糙度要求的零件时,如机器人的光学镜片安装座,可使用研磨刀具或抛光刀具进行最后的光整加工,以获得极低的表面粗糙度值。
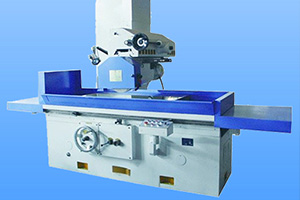
# 刀具的使用
- **刀具的安装与定位**:刀具安装时必须保证其与机床主轴或刀座的连接精度和刚性。例如,在数控加工中心上安装刀具时,要使用合适的刀柄,并确保刀柄与主轴锥孔之间的配合精度,一般采用7:24的锥度配合,以保证刀具在高速旋转和切削过程中的稳定性。同时,要精确调整刀具的位置和长度,通过对刀仪等设备进行刀具长度和半径的测量和补偿,确保刀具在加工过程中能够准确地切削到零件的预定位置,避免因刀具安装误差导致的加工精度问题。
- **切削参数的合理设置**:切削参数包括切削速度、进给量和切削深度,它们直接影响刀具的使用寿命和加工质量。切削速度应根据零件材料、刀具材料和加工工艺等因素来确定。一般来说,材料硬度越高,切削速度应越低;刀具材料的耐热性和耐磨性越好,可采用的切削速度越高。进给量要适中,过大的进给量会导致刀具磨损加剧,表面质量下降;过小的进给量则会降低加工效率。切削深度也需根据零件的结构、材料和刀具的性能来合理选择,在保证加工效率的同时,要避免切削深度过大造成刀具过载和零件变形。例如,在加工不锈钢材质的机器人零件时,切削速度一般在100 - 200m/min左右,进给量为0.1 - 0.3mm/r,切削深度为0.5 - 2mm。
- **刀具的磨损与更换**:在加工过程中,刀具会不可避免地发生磨损。刀具磨损到一定程度后,会影响加工精度和表面质量,因此需要及时进行检测和更换。刀具磨损的形式主要有磨粒磨损、粘结磨损、扩散磨损和氧化磨损等。通过观察刀具的切削刃磨损情况、切屑的形状和颜色、加工表面的质量以及切削力的变化等,可以判断刀具的磨损程度。一般当刀具的磨损量达到一定的允许值时,如硬质合金刀具的后刀面磨损量达到0.3 - 0.5mm,就需要更换刀具。同时,为了延长刀具的使用寿命,可以采用一些刀具磨损预防措施,如合理选择切削参数、使用切削液进行冷却和润滑、定期对刀具进行刃磨和保养等。
- **刀具的维护与保养**:刀具的维护保养对于保持其性能和延长使用寿命至关重要。每次使用后,应及时清理刀具上的切屑和油污,防止切屑残留对刀具造成腐蚀和磨损。对于一些精密刀具,如镗刀、铰刀等,要定期进行精度检测和校准,确保其切削精度。刀具应存放在干燥、通风的地方,避免刀具生锈和变形。对于长期不使用的刀具,可涂上防锈油并进行包装,以保护刀具表面不受损坏。此外,刀具的刃磨也需要专业的设备和技术,要根据刀具的材料和磨损情况选择合适的刃磨方法和砂轮,保证刃磨后的刀具切削刃锋利、精度符合要求。